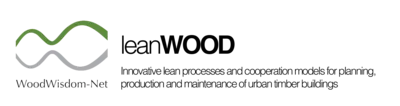
leanWOOD - a short description of the project
Modern timber architecture is associated with industrialized production of construction elements that involve a high level of prefabrication. Prefabrication is essential to ensure quality and efficiency. Each planning stage is complex, with prefabrication of off-site building elements, transport and assembling logistics increasing in order to save time during on-site assembly. The traditional way of building, which mainly focuses on on-site production has shaped the framework of organization and legislation for centuries. This process presents a significant barrier for a wider usage of timber within construction.
Specialist knowledge of timber construction and its production facilities is missing in early planning stages because timber manufacturers and/or timber construction engineers’ involvement in projects happens too late within the process. Significant expenses are incurred if a project stage is late and results in a ‘re-design phase’. This will often cause missed deadlines and eventual cost overrun. Furthermore architects and engineers are depending on consultancy by timber specialists due to the multifarious requirements and different types of timber constructions. Best conditions are given if future building projects are planned right from the start by a team of architects, engineers and timber construction specialists working together.
This is where leanWOOD starts to work! The main goal is to develop new cooperation and process models for prefabricated timber construction. “lean” represents the lean handling of processes and the efficient and effective coordination of all participants. This could be the significant collaboration needed to improve productivity in industrialized timber construction. leanWOOD refers to the basic principles of lean management- a feature of the added-value chain applied successfully in several industry sectors since 1980, with the premise here being customer focus, waste reduction and the prevention of rejects. Despite the fact that companies in the production sector have been applying the methods of lean management for a long time, these techniques and values have so far been rarely adopted by the building sector.
leanWOOD develops model solutions for the optimized workflow of cooperative planning and implementation processes in timber construction. The goal is to apply the main features of lean management to the complete planning and building process added-value chain. Based on research and analysis of existing built “best- practice“ examples and work methods of other highly developed industrial sectors, for instance ship building and automotive engineering, leanWOOD demonstrates possibilities for optimized processes and goal-orientation as well as higher value-added cooperation of project teams. Methods and models for the optimal transition from planning to production phases are achieved through collaboration between architects and engineers alongside the planning input of manufacturers.
leanWOOD - the big picture
There is a growing market momentum with stakeholders emphasizing ecological concerns and, at the same time, several European governments are currently deploying programs on building with wood. A growing community of timber manufacturers, contractors, architects and engineers are taking the opportunity to position themselves as high level competitors in the European market.
However, our sector faces a growing intrusive environment of legal frameworks, critical public perception as well as a rising economical threat which is looming to become a barrier to a successful future economic development of the wood industry.
Industrialised manufacturing methods on a high prefabrication level have drastically advanced building with wood and opened markets for the sector, especially on an urban scale. Retrospectively, multi-storey large volume new buildings as well as retrofitting using timber based solutions have been successfully realised and are now on the way to up scaling.
Due to the structure of conventional linear project processes, today’s planning and construction business often suffers from an information loss at the interface of planning and construction. In theory, linear project processes should rely on a chain of tasks from planning, production to assembly. Compared to common on-site construction off-site fabricated timber solutions demand a higher effort of planning and decision making in an early project stage.
Collaborative Design
Production planning plays a major role in the workflow. Specific knowledge on the methods of off-site production and logistics can influence design principles and the making of architecture. However, missing knowhow, the lack of understanding of partner’s needs, procurement regulations or contract details hinder an appropriate production workflow in modern timber construction and bears conflict potential between the different stages.
In consequence, project budgets often are packed by additional unpaid hours for extra communication and problem solving between architects, engineers and timber manufacturers resulting in economic unbalance.
Value chain cooperation model
In addition, current building and procurement regulations hardly allow involved producers into a design team at an early project stage. Moreover (public) procurement often leads to an economic focused decision based on the cheapest offer which is not automatically the best solution.
leanWOOD will tackle these barriers by developing concepts for lean project workflows generating higher economic, social and ecological values for all partners involved.
Research is needed to overcome the lack of process optimization through the supply and construction chain, lack of cost-efficiency, especially at operational phases, to recommend flexible regulations ensuring all safety and health aspects of end users and to improve knowledge on customer and end-users side.
In addition, there is a need for a significantly improved understanding about the behaviour of timber buildings, the integration of building services, the end users behaviour, and their requirements and satisfaction. These should be studied to develop a cost efficient maintenance management solution.